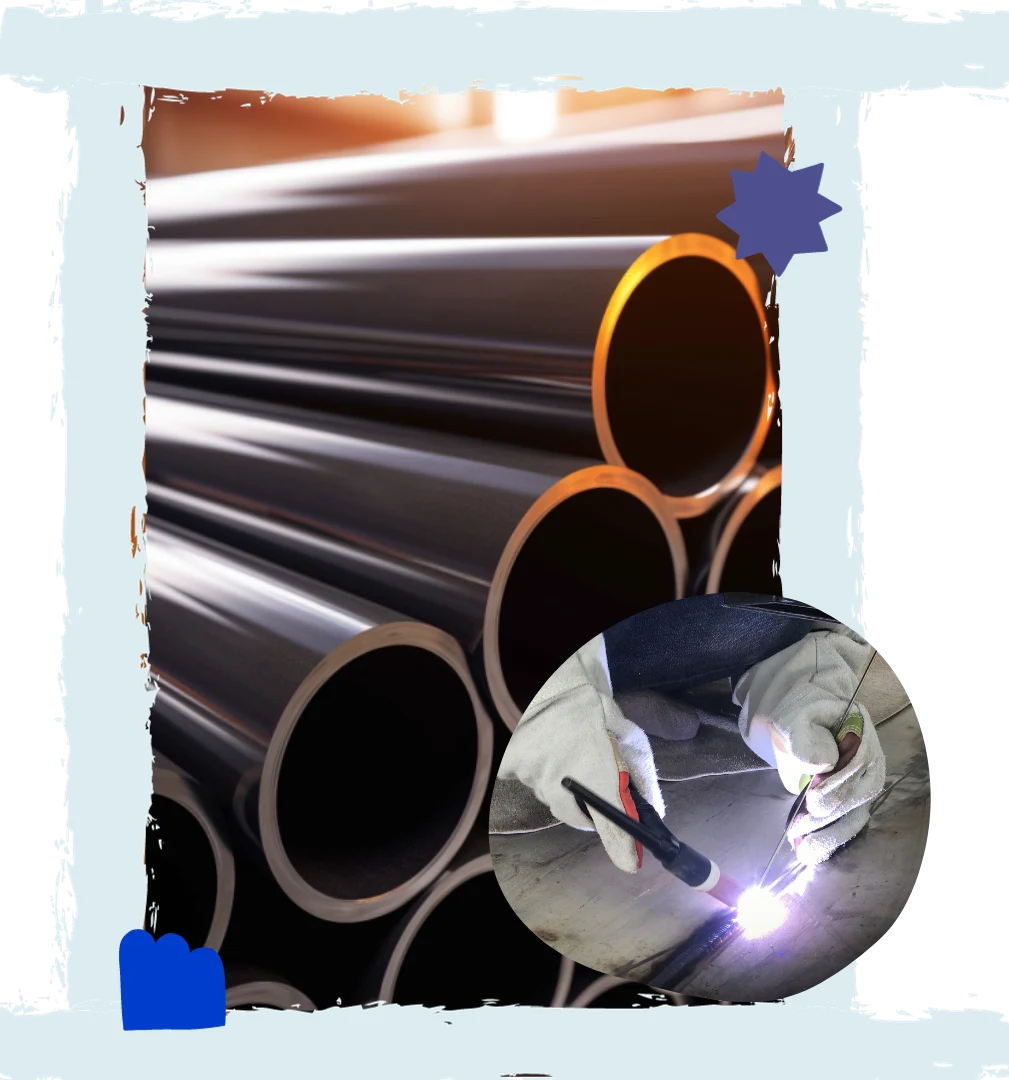
Aefab Annapurna Engineering Blog | 5 minute read
Today, Stainless Steel Fabrication or SS Fabrication is a requirement for many industrial applications. SS or stainless steel is a standard MoC (Material of Construction) in different industries for various applications where strength, durability, and resistance to corrosion are essential.
It is one of the greatest innovations in steelmaking and has many advantages over ordinary steel (mild steel/carbon steel).
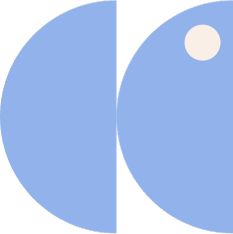
What Are The Benefits Of Stainless Steel?
The property of resistance to corrosion makes Stainless steel an excellent material for various applications exposed to liquids and other substances.
Ability to withstand extreme temperatures, durability, and hygienic properties add strength to its acceptability in the industries.
Tanks, vessels, and equipment found in the food & beverage industry, chemical processes, petrochemical industries, refineries, cryogenic storage and corrosive atmosphere are great examples.
Other industries, such as aerospace, marine, and mining, favour stainless steel due to its low maintenance cost.
Though Stainless Steel or SS has become a material of choice, this does not mean it is easy to manufacture.
The process of SS fabrication or stainless steel fabrication has significant challenges which manufacturers & fabricators find hard to solve.
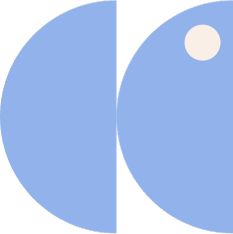
What Are The Challenges In Fabricating Stainless Steel?
There are many hurdles to manufacturing. Qualities that make it perfect for industrial application, on the other hand, pose challenges to work with during fabrication.
Stainless Steel Overheats
Compared to mild steel or carbon steel and other iron-based materials, stainless steel has a significantly lower heat conductivity.
So, it gets hotter locally while conducting metal works. Manufacturers and fabricators should take extra care to ensure heat from welding does not diminish the steel’s chemical composition.
The process of diminishment of the chemical composition through heat is called sensitisation. And since heat is necessary for most metalworking in the case of cutting or welding operations, it becomes exceptionally challenging to avoid.
How Do We Overcome These Challenges?
It is adopting good manufacturing practices while cutting, and welding that can minimise the risk of stainless steel losing its characteristics or desired properties.
One of the most effective ways to minimise the risk of overheating is to select a low-speed tool. A relatively low-speed tool does not allow the material to heat up.
Tools running at less than 4000 rpm are an excellent choice, enabling the work to continue undisturbed as long as needed.
We need to pay attention to the handling of the tool and avoid pushing it against the metal too hard, which may contribute to overheating and, in the worst case, melt the metal onto the abrasive.
The last thing you want is to commission stainless steel, only to find corrosion built up in areas of the product where sensitisation has occurred.
Stainless Steel Welding Is A Challenge
Though commonly used in manufacturing, stainless steel can present welding challenges. Keeping heat input low plays a critical role since stainless steel is less conductive than regular steel. Selecting the suitable filler metal or electrode and following proven best practices is essential for optimal weld results.
Shielded metal arc welding (SMAW), Flux-cored arc welding (FCAW), Gas Tungsten arc welding (GTAW) or TIG (Tungsten Inert Gas) are the leading processes used to join stainless steel sheets and plates. One of the most critical challenges of joining stainless steel is to ensure that the joint and adjacent material is stainless after joining.
Good Welding Practices For Stainless Steel
In addition to the proper electrode or filler-metal selection, successful stainless-steel welding requires following these best practices:
- Increase silicon levels to help with weld, pool flow and fluidity. The more sluggish weld pool of stainless steel in the filler metal, due to less fluid, can cause some issues.
- Use faster travel speeds to help keep heat input low. Slow travel speed increases heat input, burning alloying elements out of the metal and impacting weld properties, including strength, ductility, and corrosion resistance. While a travel speed of 75-200 mm/min is typical with other materials, welding stainless steel with flux-cored or metal-cored wires calls for 200 to 275 mm/min travel speeds.
- Avoid contamination of the weld using a dedicated stainless-steel brush to clean stainless welds. Using the same brush to clean stainless steel and mild steel can cause cross-contamination and rust.
- Use proper safety systems and protective gear. Some filler metals produce higher levels of weld fume than others, so it’s essential to have adequate ventilation or weld-fume-source capture in place when using them.
Achieving A Quality Finish Is Difficult
In the case of quality finish, stainless steel can be a demanding material, especially in an operating environment where other materials are being worked on simultaneously.
How To Achieve A Quality Finish When Working With Stainless Steel?
There are no shorter paths to achieve a quality finish for the stainless steel surface or welding joints. It is essential to adopt the correct process of manufacturing and material handling of the materials at the fabrication stage. It’s also necessary to use the proper tools and eliminate any risk of damage from cross-contamination.
Good fabrication practice:
- The abrasive must be changed between using it on carbon steel and stainless steel, or the remains of the carbon steel will ultimately damage the stainless steel product.
- The use of a flap disc grinder or sander disc with finer grit can deliver a better finish
Progress Is Slow
The process of stainless steel fabrication and manufacturing runs a high risk of damaging the product due to adopting the wrong procedure or tools.
How To Manage The Fabrication Pace
A careful metalwork practice can avoid this risk, but it is time-consuming. Some tasks, like grinding, and surface polishing, can slow down the entire production flow.
Adoption of a structured project management technique with work breakdown structure (WBM), identifying the interrelated activities, and analysing the critical path can bring remarkable improvement in the overall production timeline.
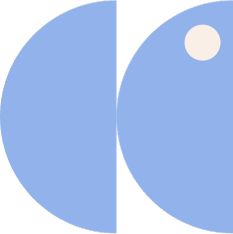
Importance Of Codes And Standards In SS Fabrication
In practice, almost all the manufacturing and fabrication processes on the shop floor are guided by national and international codes, standards, and specifications.
There are many standards like AWS – The Welding Handbook, ASM Metals Handbook, ASME Sec II, Sec VIII, Sec IX, Indian Standards and many more.
Each standard has its own set of guidelines and requirements. However, the fundamental requirements are similar in nature and generally vary with applications.
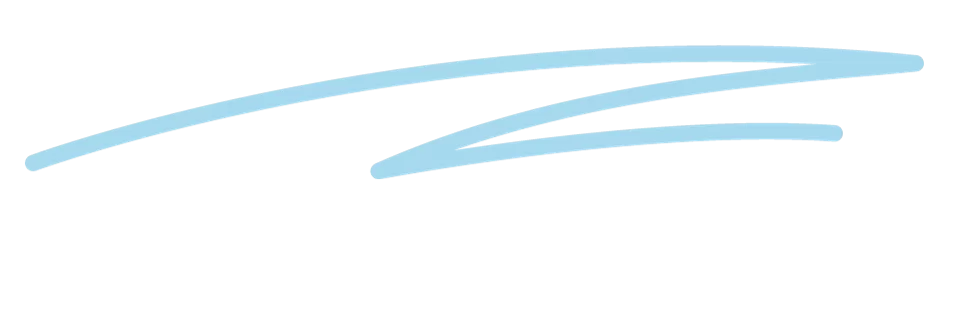
Conclusion
Stainless steel as a material of construction (MoC) is being adopted more and more across industries. From a fabrication perspective, the same qualities that make it perfect for specific industrial applications also mean that it can be challenging to work with.
Therefore, it is important to use stainless steel fabricators who have proven expertise and experience and are ready to acknowledge the additional requirements.
Share this post
About Aefab Annapurna Engineering
Aefab Annapurna Engineering has a company-wide commitment to building high-quality stainless steel tanks, pressure vessels & equipment with on-time deliveries. We are ready to go the extra mile to exceed customer expectations.
As a premier stainless steel fabrication facility in Kolkata, India, Annapurna (AEFab) has more than 30 years of experience in stainless steel fabrication that has not lost its benefits despite the challenges of the fabrication process.
More than fifty years in business have given us the knowledge, skills and experience required to safely produce high quality, custom fabricated stainless steel equipment.
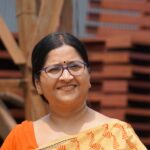
About the author
Sulekha Basu
Managing Partner of Aefab Annapurna Engineering.
Related insights
Reach out to Us
If you have anything to talk about/enquire/need support, let us know. We will go through your requests and respond within 2 business days.
Speak to us or drop us a WhatsApp message